Übergeordnetes Ziel dieses Projektes war die Entwicklung und Realisierung eines Randschichtkonzepts für Umformwerkzeuge, welches einen Verzicht auf flüssige Schmiermittel beim Kaltfließpressen von Aluminium ermöglicht. Durch quantenmechanisch geführtes Design (ab initio) von Verschleißschutzschichten mit reduzierter Grenzflächeninteraktion zum Werkstückwerkstoff wird angestrebt, den Hauptverschleißmechanismus Adhäsion (Abbildung 1) zu minimieren. Die Laseroberflächenmodifikation der Werkzeuge trägt durch die Abrundung von Rauheitsspitzen und die Randschichthomogenisierung gezielt dazu bei, abrasiven Verschleiß zu minimieren und Verschleißpartikel als Ansatzpunkte für die Adhäsion zu vermindern (Abbildung 2). Eine Bewertung der quantenmechanisch designten und laserstrukturierten Schichten, sowie deren Kombinationen, erfolgte mittels eines neu konzipierten Druck-Torsions-Tribometers (Abbildung 3) und in Fließpressversuchen im Labormaßstab (Abbildung 4).

Schmiermittelfreie Tribologiekonzepte für das Kaltfliesspressen durch interaktionsminimierte Oberflächenschichten u. -strukturen
Antragsteller: Hirt, Poprawe, Schneider (Aachen)
Werkstoffe: Aluminium
Methoden: Kaltfliesspressen
Publikationen
Stand 1. Juni 2020
SPP1676_Publications_Hirt_Poprawe_Schnei[...]
PDF-Dokument [40.6 KB]
Final Report
Abschlussbericht (in englischer Sprache)
DMFOAJ_6_2020_166-191_Teller.pdf
PDF-Dokument [4.5 MB]
Abbildung 1: Aluminiumadhäsion auf Werkzeugstahl.
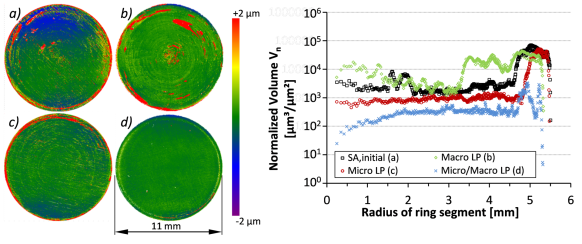
Abbildung 2: Örtliche Verteilung des adhärierenden Aluminiums nach Tribometertest auf geschliffenen (a) und unterschiedlich laserpolierten Proben (b-d) aus 1.2379+ (AISI D2).
Im Rahmen des ab-initio Schichtdesigns wurde ein neuartiges adhäsions-minimierendes Werkzeugschutzschichtkonzept vorgestellt. Dieses basiert auf einer Oberflächenfunktionalisierung mit selbstanordnenden Monolagen aus
n-Alkylphosphonsäuren, deren van-der-Waals-Terminierung zu geringen Wechselwirkungen mit dem umzuformenden Aluminium führt. Der Erfolg und die Belastbarkeit dieses Verschleißschutzkonzeptes basiert auf zwei wesentlichen Parametern der Oberflächenfunktionalisierung, die während der Bearbeitung des Projektes aufgeklärt wurden: Der chemischen Anbindung der Monolage an die Werkzeugoberfläche und der Grad der Oberflächenbedeckung des Werkzeugs mit den Molekülen der n-Alkylphosphonsäuren.
Darüber hinaus wurde eine Prozessfolge für die Laserbearbeitung von Matrizen entwickelt: Durch die Abfolge von Makrolaserpolitur zur Randschicht-homogenisierung, einer anschließenden Laserstrukturierung durch Umschmelzen und einer finalen Reduktion von Rauheitsspitzen (z. B. durch Martensitnadeln) durch Mikrolaserpolitur werden die Werkzeugoberflächen optimal für die zuvor dargestellte Funktionalisierung vorbereitet.
Abschließend konnten die Prozessgrenzen beim trockenen Vollvorwärtsfließpressen dargelegt werden.
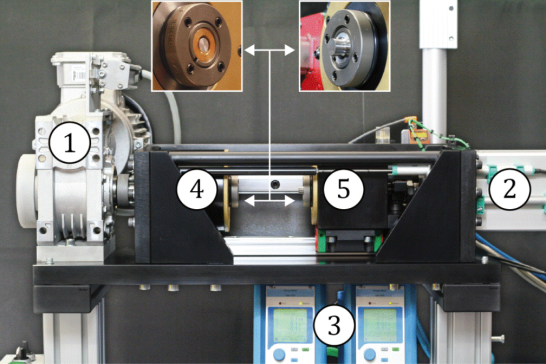
Abbildung 3: Druck-Torsions-Tribometer zur prozessnahen Charakterisierung neuer Oberflächenmodifikationen: ① Motor ② Druckzylinder ③ Dynamometer ④ Werkstückaufnahme ⑤ Werkzeugaufnahme.
English:
Lubricant-free tribology concepts for cold extrusion by interaction-reduced coatings and structures
Figure 1: Aluminium adhesion on a tool steel.

Figure 2: Spatial distribution of adherent aluminium on ground (a) and different laser polished (b-d) specimens (AISI D2; 1.2379+) after tribological testing.
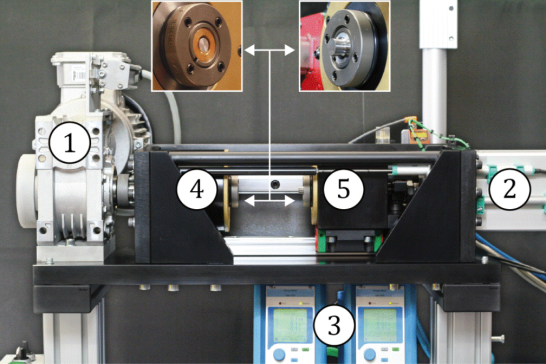
Figure 3: Compression-torsion-wear-test for process-oriented testing of new surface modifications: ① engine ② pneumatic cylinder ③ dynamometers ④ workpiece specimen holder ⑤ tool specimen holder.
IBF - Institut für Bildsame Formgebung
Name: Prof. Dr.-Ing. Gerhard Hirt
Position:
Projektleitung / project management
E-Mail: hirt@ibf.rwth-aachen.de
Description: IBF - Institut für Bildsame Formgebung
Name: M.Sc. Marco Teller
Position:
Projektbearbeiter / project team
Phone: +49 241 8095910
E-Mail: teller@ibf.rwth-aachen.de
Description: IBF - Institut für Bildsame Formgebung
LLT - Lehrstuhl für Lasertechnik
Name: Prof. Dr. rer. nat. Reinhart Poprawe
Position:
Projektleitung / project management
E-Mail: poprawe@llt.fraunhofer.de
Description: www.llt.rwth-aachen.de
Name: M. Sc. Moritz Küpper
Position:
Projektbearbeiter / project team
Phone: +49 241 8906 299
E-Mail: moritz.kuepper@llt.rwth-aachen.de
MCh - Lehrstuhl für Werkstoffchemie
Name: Prof. Jochen M. Schneider, Ph.D
Position:
Projektleitung / project management
E-Mail: schneider@mch.rwth-aachen.de
Description: www.mch.rwth-aachen.de
Name: Stephan Prünte, M.Sc.
Position:
Projektbearbeiter / project team
Phone: +49 241 80 25897
E-Mail:
pruente@mch.rwth-aachen.de